Automation has always been at the heart of the industrial revolution, and as technologies have evolved, its impact on industry and the global economy has become increasingly significant. In this article, we will explore emerging trends in automation, such as artificial intelligence, robotics and the Internet of Things (IoT), and how these technologies are shaping the future of industry and the global economy.
- Artificial intelligence (AI) and machine learning (ML)
Artificial intelligence (AI) and machine learning (ML) have become fundamental to automation in many sectors. Thanks to AI and ML, machines can now 'learn' from data and improve their performance over time, which makes them more efficient and effective. These technologies are revolutionising sectors such as manufacturing, logistics, agriculture and medicine, making it possible to automate increasingly complex tasks while reducing operating costs.
- Advanced robotics
Robotics is evolving rapidly, with increasingly sophisticated and versatile robots entering many sectors of industry. For example, collaborative robots (cobots) are becoming common on assembly lines, working side by side with humans to improve efficiency and reduce the risk of injury. Similarly, drones and self-driving vehicles are revolutionising the transport and logistics sector, offering more efficient solutions for transporting goods and people.
- Internet of Things (IoT)
The Internet of Things (IoT) is transforming industry and the global economy, connecting billions of devices and machines with each other and with the Internet. This connectivity enables greater efficiency and control in the management of industrial processes and infrastructure, improving productivity and reducing waste. In addition, IoT enables the collection of huge amounts of data that can be used to further optimise operations and develop new business models.
- Impact on employment and skills requirements
Automation has a significant impact on employment and the skills required in the labour market. While some manual and repetitive jobs are being replaced by machines, new opportunities are being created for professionals specialised in technology and high value-added sectors. It is crucial, therefore, that workers adapt to these new challenges by developing digital skills and problem-solving abilities to remain competitive in the labour market.
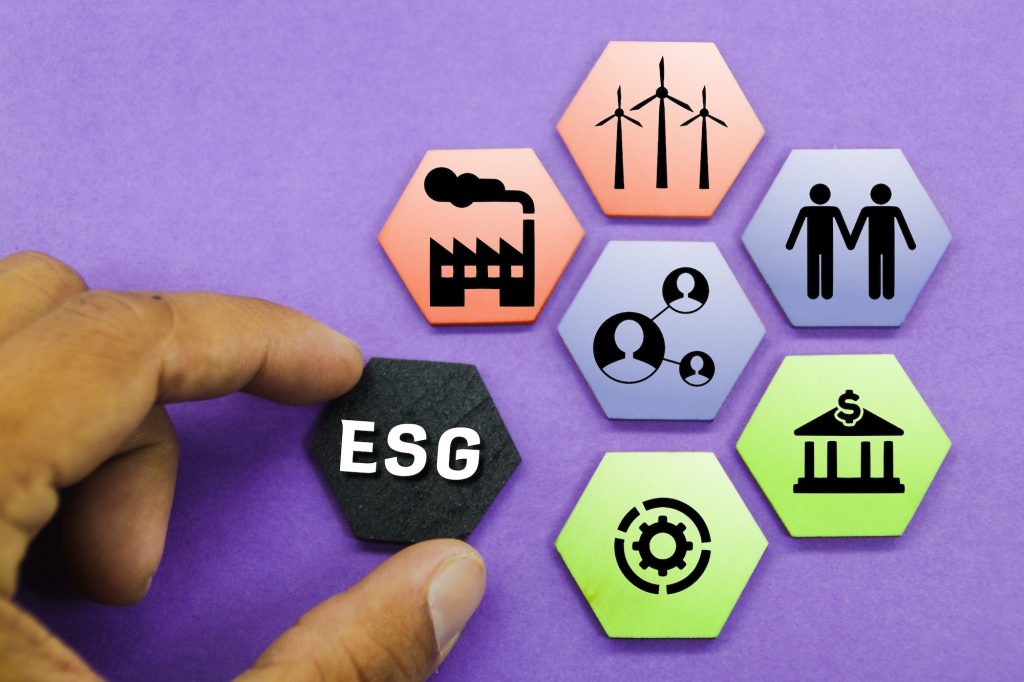
- Sustainability and environmental impact
Automation and associated technologies can help create a more sustainable future. Energy efficiency, waste reduction and optimisation of production processes are just some of the areas where automation can have a positive impact on the environment. For example, precision agriculture using drones and IoT sensors can reduce the use of fertilisers and pesticides while improving crop yields.
- Ethics and safety in automation
As automation becomes more pervasive, ethical and safety issues emerge that require special attention. It is important to ensure that automation technologies are used responsibly, respecting the privacy, safety and rights of workers. Furthermore, it is essential to develop regulations and standards that ensure the safety and reliability of automated systems, particularly in critical sectors such as medicine, transport and energy.
- IATF 16949:2016 requirements and automation
IATF 16949:2016 is an international standard that sets out the requirements for a quality management system (QMS) specifically for the automotive industry. This standard was developed by the International Automotive Task Force (IATF) with the aim of harmonising the various quality management systems used by automotive manufacturers and component suppliers worldwide.
In terms of automation, IATF 16949:2016 places special emphasis on the importance of ensuring that automated processes are designed, developed and maintained to meet quality and compliance requirements. Some of the key aspects of automation covered by the standard include:
- Risk assessment: Organisations are required to carry out appropriate risk assessments for automated processes in order to identify and mitigate any hazards to product quality, worker safety or the integrity of the system itself.
- Process control: Companies must establish and document process control methods for automated systems, ensuring that these are monitored and adjusted to maintain a consistent level of quality.
- Maintenance and Calibration: It is essential to ensure that instruments and equipment used in automated processes are maintained and calibrated regularly to ensure their reliability and accuracy over time.
- Staff training: The standard requires organisations to ensure that staff involved in automation have the necessary skills and knowledge to understand, manage and maintain automated systems effectively.
IATF 16949:2016 recognises the importance of automation in the automotive industry and lays down strict requirements to ensure that automated processes are managed responsibly and in accordance with the highest quality standards. By integrating these requirements into their quality management systems, automotive companies and their suppliers can further improve the efficiency and quality of their products, helping to shape the future of automation in the global automotive industry.
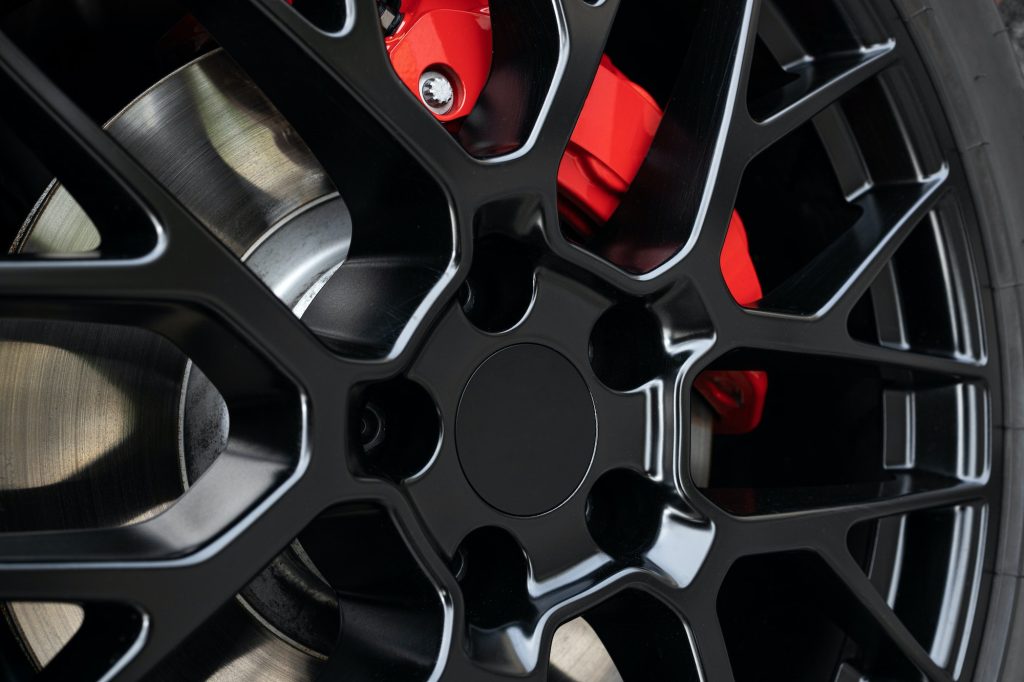
Automotive supplier case study
Let's look at a practical example of the application of IATF 16949:2016 requirements for an automotive supplier.
Company XYZ is a supplier of automotive components, specialising in the production of braking systems. To ensure compliance with IATF 16949:2016 requirements and to ensure that its automated processes are managed effectively, the company has implemented the following actions:
- Risk assessmentXYZ conducted a thorough risk assessment of the risks associated with its automated processes, identifying potential hazards to product quality, worker safety and system integrity. As a result of this assessment, mitigation measures were taken, such as the installation of additional safety systems and the implementation of emergency protocols.
- Process control: To ensure optimal control of automated processes, XYZ has developed and documented detailed procedures for monitoring and adjusting key process parameters such as moulding pressure and material temperature. This ensures that the components produced always meet the quality standards required by customers and regulations.
- Maintenance and Calibration: The company has implemented a regular maintenance and calibration programme for the equipment and instruments used in automated processes. This includes periodically checking the accuracy of measuring machines, replacing worn components and updating the software of control systems to ensure optimal performance and long-term reliability.
- Staff trainingXYZ invests in the training of its staff, ensuring that employees involved in automation have the necessary skills and knowledge to manage and maintain the systems effectively. This includes training on the basic principles of automation, the use of control systems and troubleshooting, as well as specific training on the technologies and processes used in the company.
- Supplier Management: In accordance with the requirements of IATF 16949:2016, XYZ has implemented a supplier evaluation and selection process to ensure that the materials and components used in production meet the required quality standards. The company regularly monitors supplier performance and conducts periodic audits to ensure compliance with regulations and quality standards.
- Change ManagementXYZ has developed a change management system to ensure that changes to production processes, product specifications or customer requirements are managed effectively and in a timely manner. This system includes assessing the impact of changes, communicating with stakeholders and training personnel involved in the change, ensuring that product quality and process efficiency are maintained during the change process.
- Monitoring and continuous improvementXYZ has implemented a continuous monitoring and improvement system, using key performance indicators (KPIs) to assess the effectiveness of production processes and identify areas for improvement. By analysing the data collected and applying problem-solving techniques, the company is able to make continuous improvements to its automated processes, further reducing costs and increasing product quality.
By implementing these measures in line with the requirements of IATF 16949:2016, XYZ has significantly improved the efficiency and quality of its production processes while reducing risks to worker safety and the environment. Moreover, compliance with these standards assures customers and business partners that the components supplied by XYZ meet the highest expectations in terms of quality and reliability, strengthening the company's reputation in the automotive industry.
Conclusions
The future of automation in industry and the global economy is fraught with opportunities and challenges. The adoption of technologies such as artificial intelligence, robotics and the Internet of Things will lead to greater efficiency, productivity and sustainability in many sectors. However, it will be crucial to address ethical and safety issues, as well as to ensure that workers are properly trained and prepared for the new skills required in an increasingly automated world.
To keep up to date with the latest trends and developments in automation, be sure to follow our blog www.automodemy.com and to subscribe to our newsletter.
0 Comments